F56 JCW/S Brake Cooling Kit
- George Tsakonopoulos
- Jan 10
- 3 min read
Our objectives for this product are pretty simple:
Creating the highest performing cooling kit for the F56 MINI, utilizing high tech manufacturing solutions while making a truly plug and play kit.

The F56 JCW and S models from factory utilizes openings in the front bumper to cool the brakes. These openings direct air into the wheel arch and that's pretty much the cooling solution by MINI. This method might be satisfactory for street or light spirit driving but it becomes fast incapable to cool down the brakes in high stress scenarios like when you drive your car in a race track.
In high end race applications cold air is diverted in the center of the brake disk. This is the most efficient way to cool down your brakes. Reason is that the internal veins of the brake disk acts like a fan pulling air from the center and expelling it from the outer edge. This is even more effective withe aftermarket brake disks, where the cooling veins are optimized for center feed cooling.
With that said, the kit should:
-Direct airflow in the center of the brake disk for maximum cooling.
-And of course, be plug & play as it will be used in road legal cars.
First step: 3D scanning
We 3d scan the suspension assembly in various positions. This way we have the full suspension movement envelop. We had to take in consideration the far left and right positions as well as full compression and extension of the suspension components.

Admittedly, the available space is limited. Designed the kit around a 225/40/r18 (original setup is a 205 tyre) without the use of spacers makes things even more challenging.
Below you can see our 3D model, utilizing the original wheel arch openings to draw cold air.

The kit uses two airducts (black colour) and a redesigned back plate for the center air feed.
The back plates have very similar geometry to the original ones with the addition of an central air feed. This back plates will be 3D printed in aluminum.
Once CAD (engineering design) was finished we 3d printed all the models and made our first test fitment.
Non working prototypes:

Production models:
The air ducts are lightweight and very durable, made out of nylon 12 same as our record in sales R53 charge pipe kit and intake manifold.

Back plates 3d print in aluminum, with center air feed:

The complete kit with all the air ducts and the 3d print aluminum back plates.

Of course reaching this point was not easy and we had to do lots of revisions to make sure there were no clearance issues. And when we say lots of revisions we mean it:

Developing a product is not easy. Especially when you are trying new ideas and manufacturing methods.
For example: we tried many variations for the metal 3D printed back plates, with different thickness and print orientations in order to achieve the results we wanted.
We believe the back pates look amazing!
Lets us know what you think.

Production prototype tested on our demo F56 JCW:
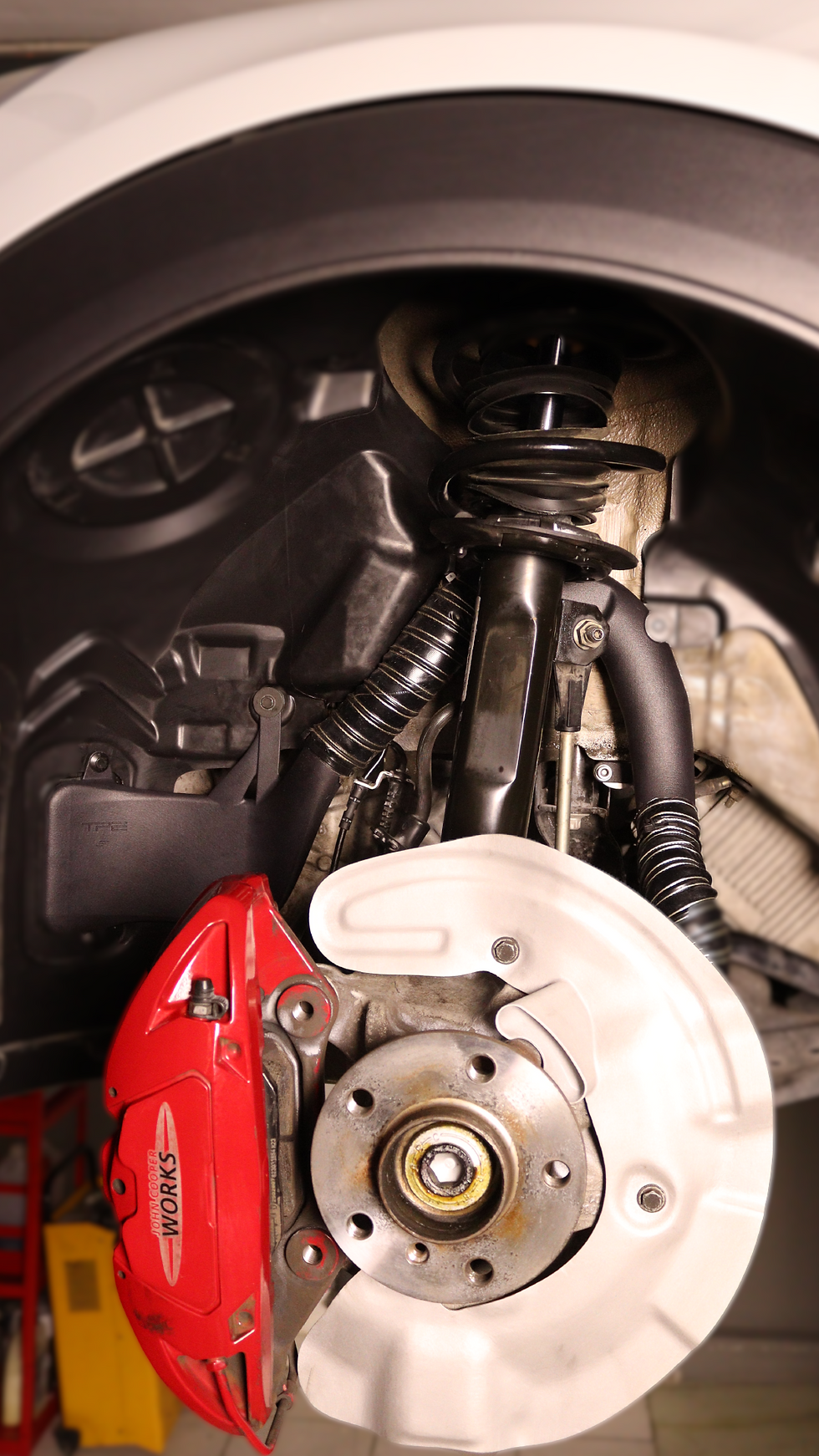
In order to visualize the air flow we used a smoke machine, feeding smoke at the front of the car (bumper opening):
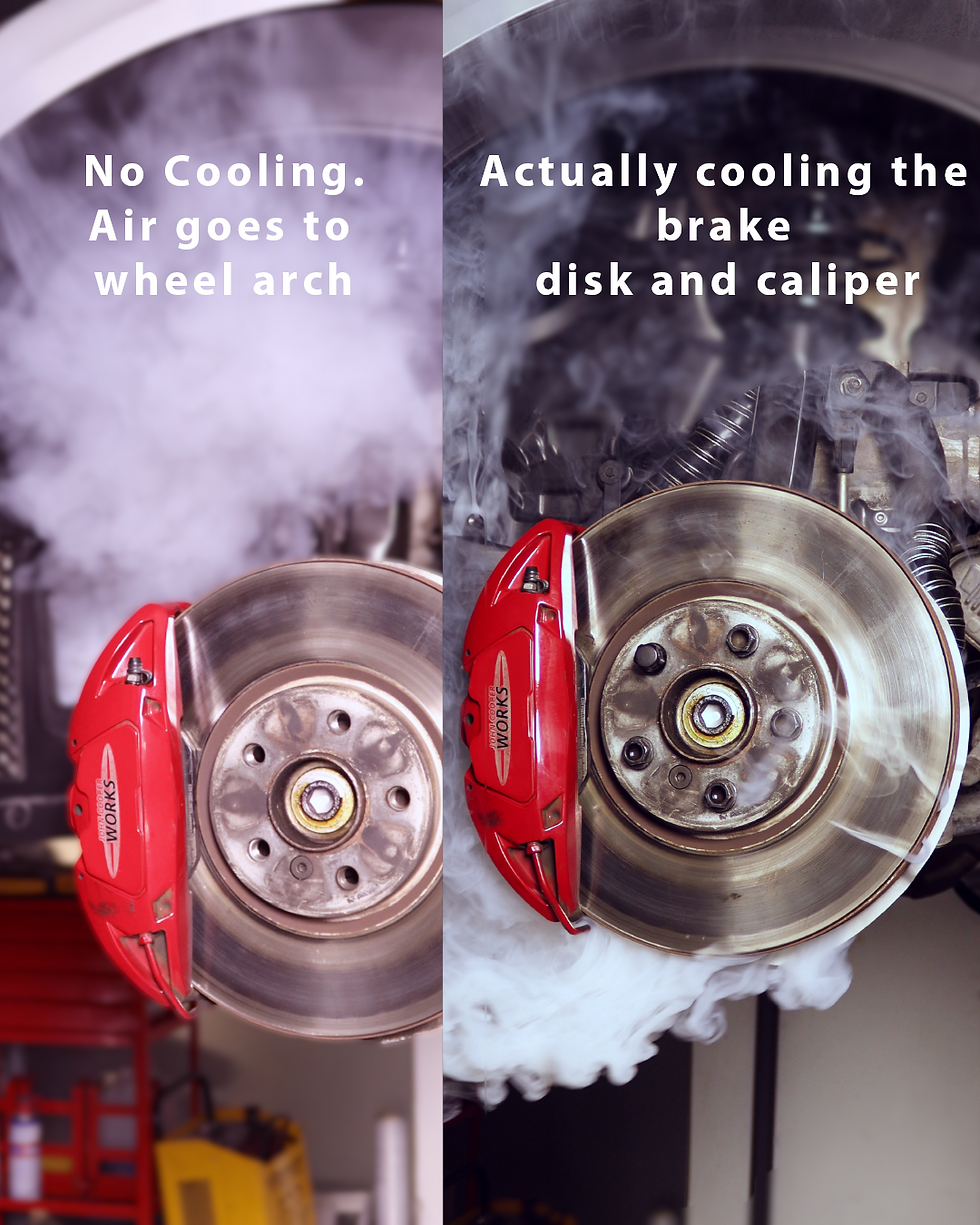
Thermal testing:

Test results are very positive with clear difference in the temps with our kit installed.
First test, we installed the kit only in the left hand side so we have a direct comparison of the two sides. Then we repeated the same in the right hand side.

So all looks good. The kit works and does cool the disk brakes better than the original setup but... we want to test the kit with double center air feed!
Stay tuned for the next blog post as this is turning fast into an engineering exercise!!
Comments